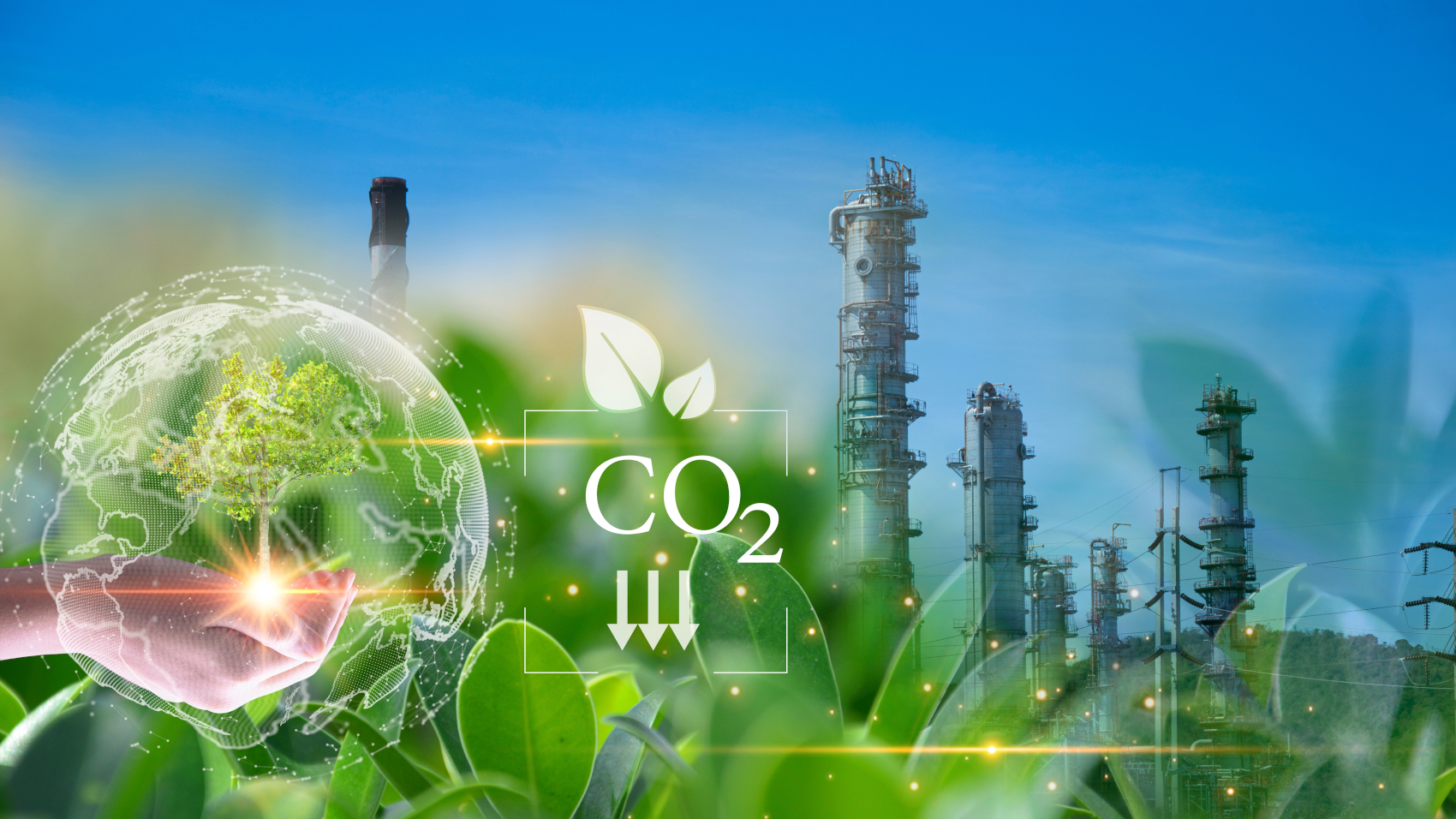
Towards a More Sustainable Chemical Industry: the SunCoChem Project
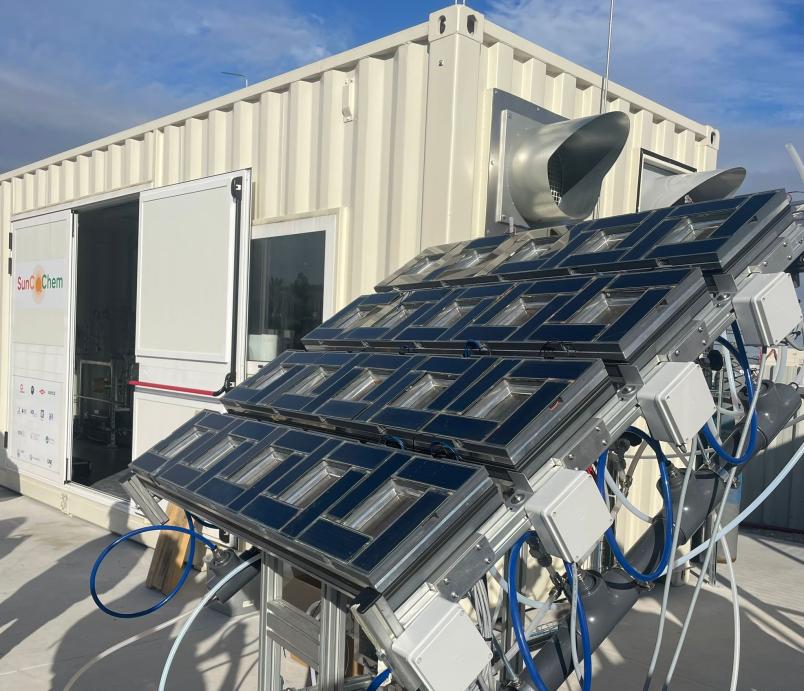
The European SunCoChem project, aimed at producing chemicals from renewable sources, officially concluded on 31 October. This initiative envisions a sustainable and innovative future for the chemical industry, emphasizing the use of renewable resources such as solar energy and carbon dioxide (CO2) from industrial waste.
Led by Simelys Hernández, professor at the Department of Applied Science and Technology-DISAT, Politecnico coordinated the project's technical development. The CREST team successfully integrated system components to capture and convert CO2, building on their experience from prior European projects. The primary goal of SunCoChem was to create an innovative device capable of autonomously capturing and converting CO2 into sustainable chemicals in a single, integrated unit.
The reactor prototype demonstrated at Technology Readiness Level (TRL) 5 shows promise in reducing costs and CO2 emissions, enhancing the efficiency of solar energy conversion for chemical production, and significantly decreasing the European chemical industry's reliance on carbon-based raw materials.
This “artificial leaf” could lead the sector toward a more sustainable future. The reactor will specifically be tested for producing three valuable substances for the European chemical industry, useful in cosmetics and food: LimoxalTM, Valeraldehyde, and Glycolic Acid.
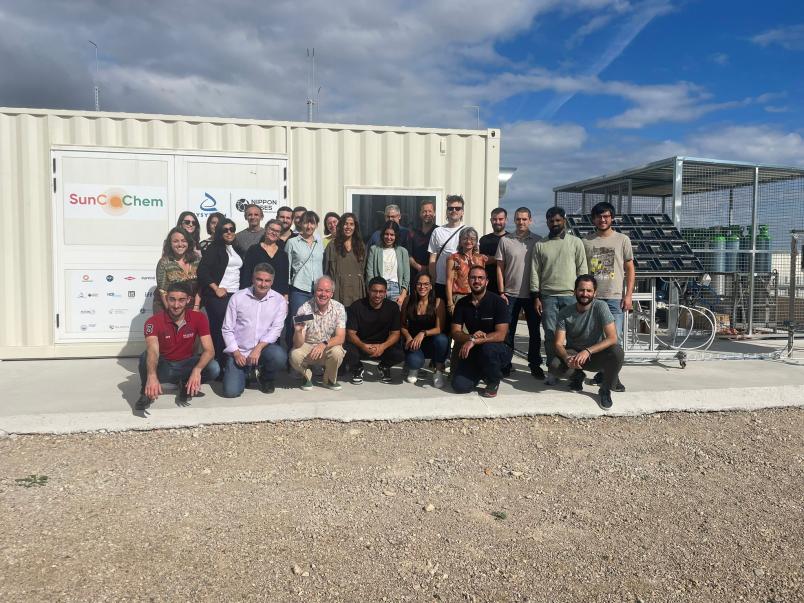
As Simelys Hernández noted, “SunCoChem addresses critical challenges currently hindering photo-electro-synthesis processes and goes beyond the state of the art to develop and validate new, efficient, and scalable production routes. In their role as technical coordinators, the team developed the cathode electrode and successfully scaled its production to 100 cm². They were also pleased to define the specifications necessary for integrating cell components, optimizing operational conditions, and demonstrating their performance at relevant levels (TRL 3/4). The CREST team contributed to validating the TRL 5 prototype, which features a 0.2 m² active area in the photo-electrochemical system, making it the largest of its kind in the world and bringing this cutting-edge technology closer to real-world application”.
Funded under the European Union's Horizon 2020 programme, the project comprised a multidisciplinary consortium of 14 partners from eight European countries, including EURECAT – project coordinator and responsible for developing innovative catalysts – Helmholtz Zentrum Berlin – studying photoanode materials – the Italian Institute of Technology – developing CO2 capture membranes and advanced characterization – and the French National Centre for Scientific Research (CNRS) – developing ion exchange membranes. The consortium also included small and medium-sized enterprises like Solaronix, Avantium, Laurentia Technologies, and IOLITEC, which contributed to material development and scaling up production. Hysytech, an engineering company, built the prototype and TRL 5 plant, while chemical companies like DOW and IFF provided process and product specifications. Additional partners such as the Spanish Association for Standardisation (UNE) and the International Hellenic University supported standardisation and social acceptance.